Liquid slurry irrigation in fields using tankless hose systems
When farms are seriously struggling with soil compaction, heavy tankers used to fertilise fields with slurry also come under fire. Some German farms, concerned about their soil health, use hose systems, which are lighter in weight compared to bulky tanks.
Less pressure on the soil is the main argument in favour of hose systems. A self-propelled machine with a hose and slurry in it weighs around 12 tonnes, while a tractor with a slurry tank weighs up to 25 tonnes. The hose-driven self-propelled machinery has 1050 mm wide wheels, all of which are driven. When fully loaded, large self-propelled machines without hoses for liquid manure application weigh around 70 tonnes. The difference in the pressure exerted on the soil is obvious.When the soil is so wet and waterlogged that heavy implements cannot be used, hose systems are said to be just what the doctor ordered. However, their weight is outweighed by the time it takes to prepare the hose systems for the job.
Two types of hose for slurry application
Logistics are greatly simplified by a special container with pumping station. The container serves as an intermediate slurry storage. Farms try to move as little as possible into the container, so as soon as the drum hose reaches its fertiliser dose, additional hoses are used to irrigate the slurry over longer distances. These are called flat hoses, which have a diameter of 6 inches (more than 15 cm) when pressed by the feed material. The hoses arrive at the point where the organic matter is added, folded on low-frame trailers. Hoses of 100 & 200 m can be combined into a single system up to a total length of 1 kilometre.
For example, UAB „interAG“ offers Austrian systems that can be distributed over distances of 5, 8 or even more kilometres.
An additional worker is employed in the field alongside the tractor driver to carry out the spreading and dismantling of the slurry delivery systems, as well as to control the slurry irrigation. Thanks to long hoses, the farm provides slurry irrigation to the fields at a distance of 3-7 kilometres from the point of pumping the slurry into the system. But depending on the characteristics of the liquid manure, an additional pump must be installed at a certain distance to maintain pressure.
In addition to hose systems, a disc harrow or a strip cultivator can be used to spread and incorporate the liquid slurry into the soil. If the hose is routed over a passable road, it is protected by a special bridge to prevent the hose from being run over by passing machinery.
The hoses on the reel of the machine, which are responsible for the direct irrigation of slurry, have a diameter of 4.5 to 5 inches and a length of 550 to 630 m. The hoses can be spread and folded up to within 12 m of the tractor by means of a special rigid adapter.
With their telescopic ašs, the reels „run“ in the fields behind the tractor's passages and therefore cause less damage to the soil structure. In rough terrain, the tractor is used in conjunction with a cultivator for strip-till technology.
By the way, self-propelled machines with special tyres can apply liquid fertiliser right up to seedling emergence. It is important to make sure that the lower 50 cm of the hanging distribution hoses are made of a harder and heavier material to allow the fertiliser to be applied without deviating from the spreading path.
Hose systems working details
Slurry fertilisation starts at the edge of the field, when the hose has already been spread. The adapter then guides the hose, running it parallel to the movement of the equipment. When the tractor is working in conjunction with the cultivator, the hose is routed 12 metres away from the tractor, and in self-propelled systems, through the centre of the swath. In reverse, the hose is reeled in. It is important to work delicately here, taking care not to rub the hose against stones, to move it little, or to stretch it across the crop – this will not be good for the crop or the hose. The dosing of the slurry is controlled by on-board electronics, depending on the rolling speed.
As for the operation of the pump in the hopper, the operator can switch it on and off remotely. During the turning operation, the pump is normally not switched on to maintain the pressure in the system and the liquid slurry supplied is collected in a small front intermediate tank mounted on the tractor, which is further distributed according to the dosing standards at the end of the turning operation.
In fields up to 1 km long, work is carried out on two sides. Longer fields require a mid-field turn. But as the manoeuvre is carried out only by the unit responsible for spreading the fertiliser, there are no deep traces in the field after the turning point. Applying slurry to the field using hose systems is no different from tanker technology.
Theoretically, a hose system can pour up to 240 cubic metres of slurry per hour, but due to the time required to assemble the entire system and make the turns, the realistic output is around 150-180 cubic metres per hour.
The turning of the tractor and implement is done by lifting the implement with the injectors. If the liquid organic fertiliser supply is not interrupted, it will continue to flow into the injectors and will spill out at the edge of the field, at a rate of 1,5 to 2 m³ per manoeuvre. Closing the valve and blocking the flow increases the load on the couplings and the hose and provokes a hydraulic shock when the valve is opened at the end of the turn.
The front tank has performed well, avoiding slurry spreading on the field edge. This is because when lifting the implement with injectors, making a turn or any other manoeuvre, the operator switches the liquid slurry supply from the injector to the front tank. The slurry flows into it for the entire time required for the turn. When the manoeuvre is completed and the injectors are returned to the working position, the operator switches the slurry supply.The slurry is pumped out of the slurry tank and fed to the injectors. The capacity of the front tank is sufficient for normal manoeuvring, even at high slurry irrigation rates.
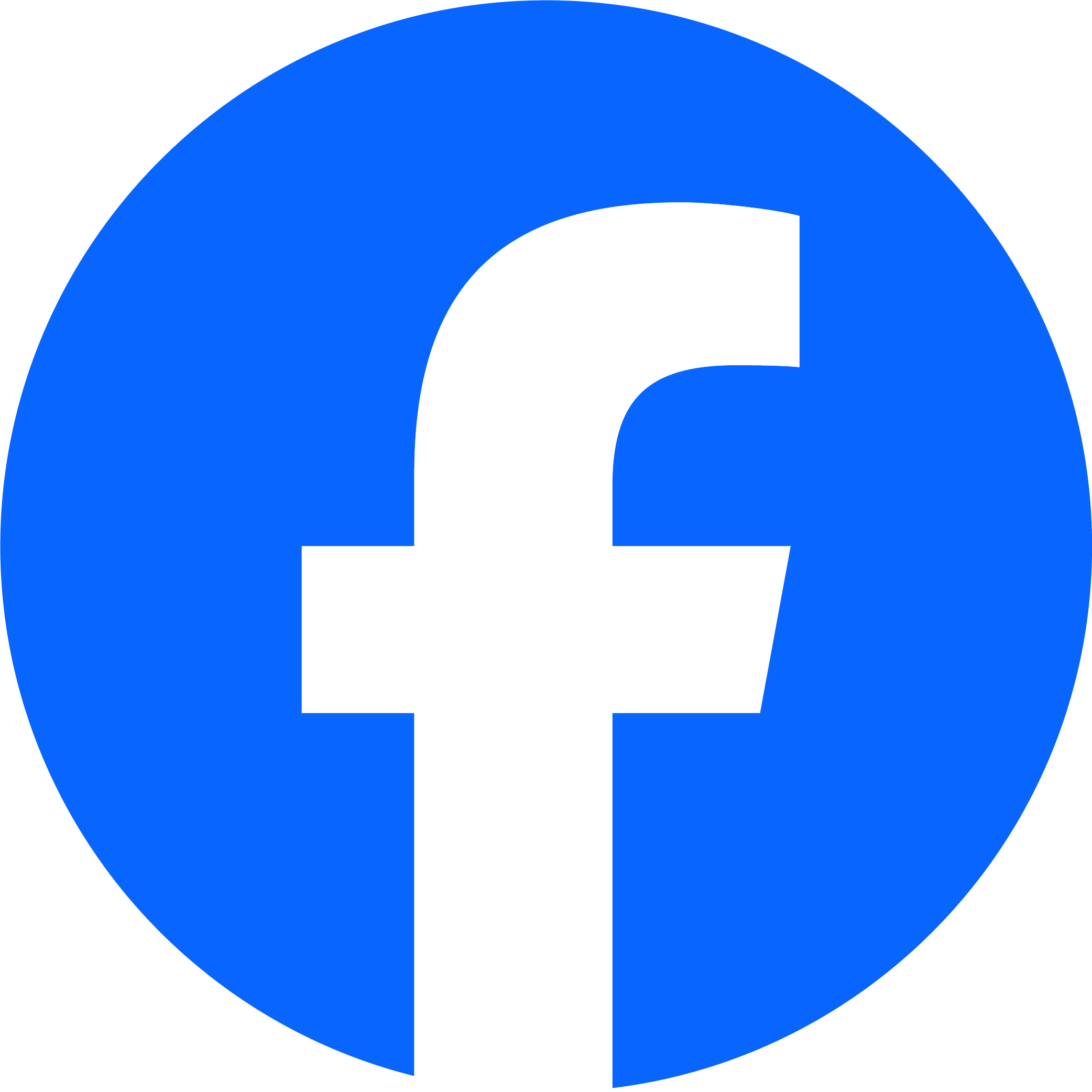